Best Ways to Reduce Warehousing Costs in 2023
- Share
- Issue Time
- Jun 29,2023
Summary
With enough knowledge, you can save more per hour on order volume. This article covers warehouse costs and ways to reduce them. let's start.
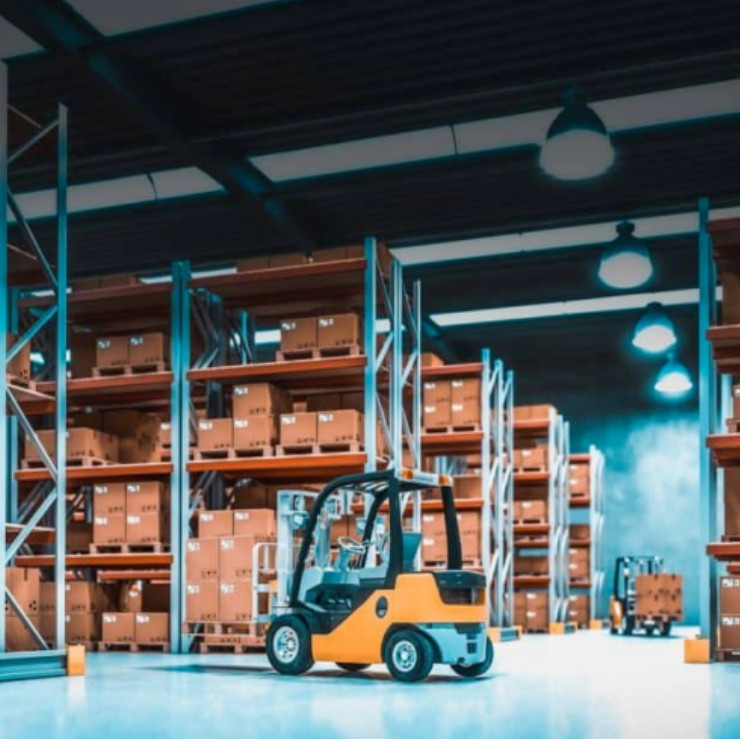
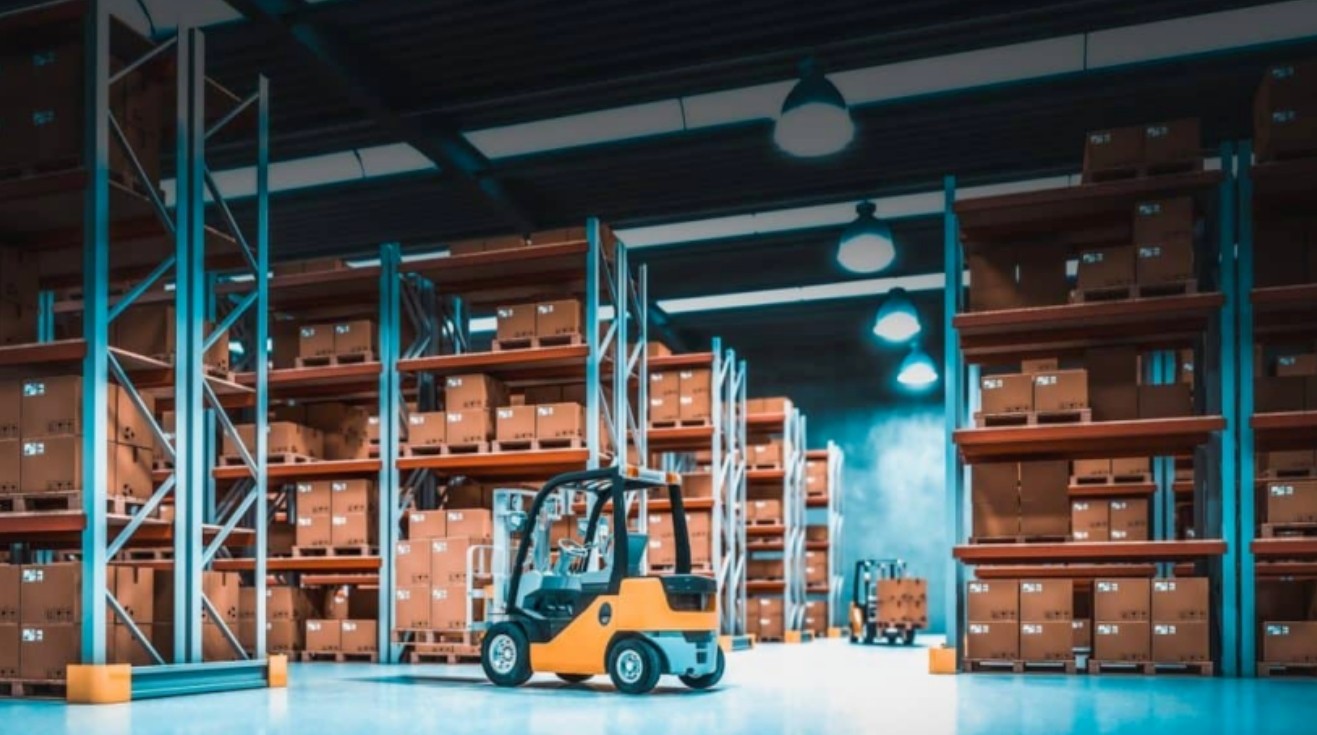
E-commerce business owners need to deal with the many operating expenses associated with their business. Warehouse operations require certain costs.
As seasoned procurement professionals, we have worked with clients who question these costs. You will get a solution on what you need to pay for purchasing warehouse space.
With enough knowledge, you can save more per hour on order volume. You can also learn about the differences between different fulfillment services.
This article covers warehouse costs and ways to reduce them. Let's start.
What Are Storage Costs?
A warehouse is a large building that can store a variety of goods. They usually require a certain outlay.
Warehousing costs generally refer to the management costs required by the warehouse. It includes operating expenses such as salaries, utilities, and equipment removal.
However, different companies will have different costs. They vary in the amount of storage they handle and the size of the warehouse. In addition, security management is also part of the fee.
Types of Warehouse Costs
There are 4 types of warehouse costs. Let's see what it is.
Deal With
It is the largest cost in warehousing costing. It includes receiving, putaway, order picking, and loading of goods. Handling costs can be minimized through packaging optimization and the selection of small packages.
The equipment used in the warehouse is also part of the handling fee. It is related to the electricity used to power the device. The goods here are called "dynamic goods".
Storage Pricing
Goods in storage are called "stationery goods". They will charge even if the goods are not moved. Customers can choose dark storage near the city to get lower storage prices.
Usually, the cargo fee is charged by pallet, which is called the monthly fee after accumulation. Fees include expenses for occupancy of the facility. If the entire building is used, the facility is subject to a gross occupancy fee.
Operations Management
Operations within the warehouse also require costs. Operating expenses are linked to employee salaries. Employees such as clerks and workers are subject to operational management. There are also costs such as information technology, supplies, and insurance.
General Administrative Expenses
General and administrative expenses are indirect. They are not included in the operating fee. For example, salaries of non-business personnel and general office expenses. These costs are allocated by the head office of the organization.
How to Calculate Your Space Requirements?
To calculate the total cost of warehouse space, you need to calculate the space. Here are the calculation steps you can take:
1. Stack All Goods Side by Side
The less need for warehouse space, the lower the storage costs. You can compress cargo so they take up very little storage space.
After compacting the cargo, it needs to be measured. You must measure the height, width, and length of the stack.
2. Multiply by the Length of the Stack
Multiply the length and width of the pallet storage. The final number is the total square footage you need for storage.
3. Multiply the Square Footage by the Height
You must measure the highest point of the stack of pallets. You can then multiply that number by the calculated square footage. This will be the required warehouse space per cubic foot.
4. Divide Numbers by Size
Once you've figured out the square footage, you'll need to divide it by the cubicle or locker. For example, the Bay Area is 250 square feet. But you have 500 square feet of cargo. So you need to divide your goods into two compartments.
How Are Warehouse Costs Calculated?
According to different storage costs, the fee is also different. You can view the different types of costs listed here.
Space Cost
After calculating the storage space, you can calculate the storage space according to the rate. Some companies charge storage space costs by square feet, cubic feet, or intervals.
Base Rental Rate
Rent will be calculated on an annual or monthly basis. This cost does not change based on the warehouse space used. Therefore, it is a fixed cost in warehousing costs. Some landlords offer discounts if you rent annually. These rates vary by location, so I try to choose cheap storage space.
Estimated Operating Expenses
Operating expenses include triple network (NNN) or common area maintenance (CAM) costs. The total cost is usually property taxes and insurance. It also includes typical area maintenance costs, such as cleaning or repairs.
Additional Warehouse Costs
Additional warehouse costs include utilities used in the warehouse. Water, electricity, cleaning and maintenance services are all part of the fee.
Ways to Reduce Warehouse Costs
There are various ways to reduce warehouse costs through improvements.
Inventory Visibility
Inventory visibility and other responsibilities are overlooked by most companies. But picking and packing is easy if workers know where the inventory is stored. With shorter delivery times, you can reduce storage costs.
Storage Optimization
The most common way to reduce costs is storage optimization. You can adjust physical structures, warehouse processes, product placement, and retrieval methods.
In this way, the flow of inventory will be efficient. Optimizing the efficiency of your warehouse can help you save on storage costs.
Anti-Theft
Theft can cause you to lose money. But if you take precautions, you can probably avoid losses. You may consider using specific system apps for prevention. It includes worker schedules or storage checks.
Cross Transport
Cross-docking helps save money because it cuts out the middleman. It can send products directly to customers.
You don't need a middleman for delivery. It reduces routing costs, which in turn reduces warehousing costs.
Effective Slotting
Slots are where you categorize and organize your inventory. By optimizing your processes, you can increase the productivity of your warehouse. When productivity increases, it will help you save on your budget.
Optimize the Picking Process
The picking process takes a lot of time, especially in large warehouses. Workers spend a lot of time retrieving products.
You can optimize the picking process by reducing the time taken. Also, it helps if you stock up on emergencies. Make sure to store popular products in a closer area than slow products.
Benchmarking
Benchmarking can help you understand problems in your warehouse. Warehouse processes can be corrected if benchmarked. They will streamline their workers to keep them on track. Customers will be happy, which will increase your profits.
In short, you will incur many expenses in the warehouse. It includes operations, management, payroll, and maintenance services. They are critical to ensuring efficient warehouse operations.
You need to be aware of such fees to avoid the loss of your business. Still, even with outsourced services, there are ways to reduce them. With careful planning, you can better optimize your bottom line.
We hope this article shared all the information you need about warehouse costs. If you have any questions, please feel free to contact us.
RND is a professional China sourcing agent. Our original idea is to help foreign friends solve communication problems with Chinese factories and be responsible for the quality control of production. As demand for this service continued to increase, it became our main business. Over the past 16 years, we have built trusting relationships with clients from more than 50 countries. With our help, more and more of their products are featured and bestsellers on Amazon.